
Printing ink on tinplate cans requires good adhesion and mechanical properties to withstand the multiple processes involved in making food tins, tea cans, and biscuit cans. The ink must adhere firmly to the metal plate and possess the corresponding mechanical strength.
To improve the adhesion properties of the ink, white ink must be printed on the tinplate cans before the colored ink is applied. White ink is the basic tone for printing patterns and has high luminance. After adding other high-energy inks, the luminance of all colors can be enhanced, thus forming a complete color spectrum.
When printing on tinplate cans, white ink or primer must be applied before the color printing because the surface of tinplate cans is silver-white or yellow with a metallic luster. To ensure the quality of white printing, there must be good bonding between the white ink and the primer. The ink must withstand multiple high-temperature baking without yellowing and resist fading from high-temperature steam. Applying the primer can improve the adhesion of the tinplate can and enable better attachment of the white ink to the surface. Typically, epoxy amine primers are used because of their light color, aging resistance, good elasticity, and ability to withstand impacts. Two layers of white ink are usually required to achieve the desired whiteness.
In the process of printing on tinplate cans, the drying process of the ink is critical. Since the surface of tinplate cans cannot use water permeable solvents, heat-curing drying is usually used. This drying method heats the ink to evaporate the volatile components, allowing the resin, pigment, and additives in the ink to crosslink, forming a strong and dry ink film.
During the drying process, the ink must withstand high temperature and high humidity environments, so the requirements for the ink's properties are also higher. In addition to the basic properties required by general offset inks, these inks must have heat resistance, strong ink film adhesion, impact resistance, good hardness, boiling resistance, and lightfastness to ensure the quality and service life of the printed product.
In conclusion, the drying process of ink in tinplate can printing has a significant impact on the quality of the printed product and must be carefully designed and controlled. Only by choosing the appropriate ink and drying method can the quality and reliability of the printed product be guaranteed.
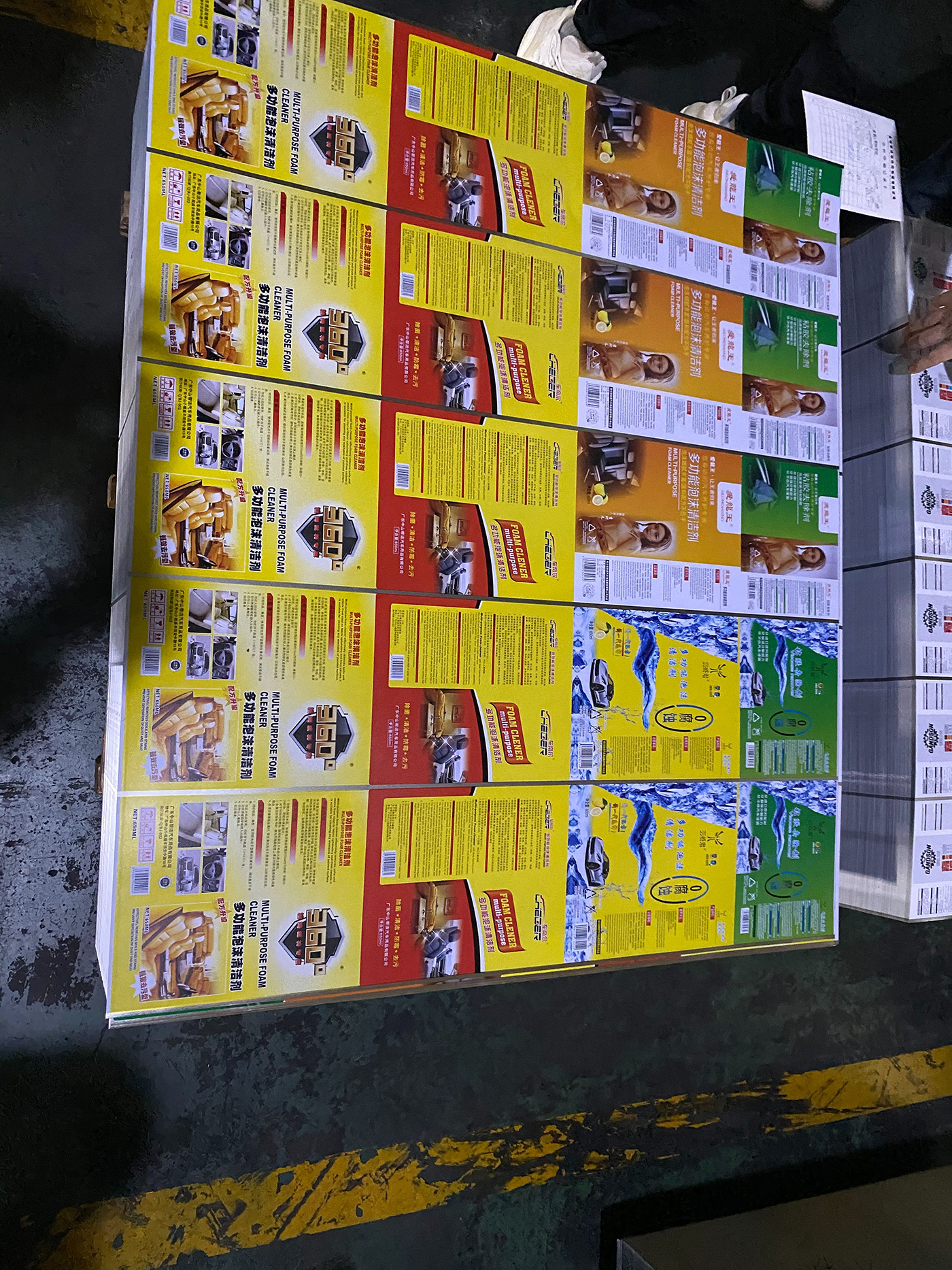
Post time: Mar-06-2023